Бизнес-план: Изготовление шашек для поддонов
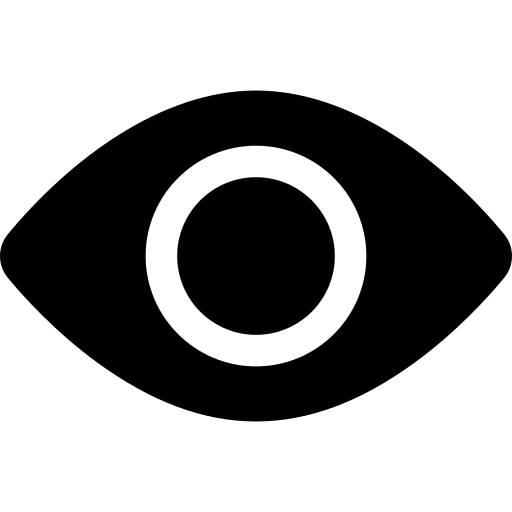
Шашкой, или бобышкой, называют кубик, соединяющий верхнюю и нижнюю часть складского поддона. Мы считаем, что данное производство сейчас является очень актуальным и интересным, а вы скорее всего мало что о нём слышали, поэтому сперва расскажем, почему наш выбор пал именно на этот вид бизнеса. И начнём с события, которое явилось катализатором для роста эффективности любой переработки опилок.
Дело в том, что распоряжением правительства от января 2018 года опилки отнесли к отходам пятого класса опасности, в связи с чем предприятия деревообрабатывающей промышленности моментально стали обязаны утилизировать или перерабатывать древесные отходы в срок 11 месяцев, иначе им будут грозить крупные штрафы, вплоть до приостановки деятельности.
Внезапно возник вопрос, как эти отходы утилизировать, ведь мусорных полигонов, готовых принять опилки – считаные единицы. Компании начали искать варианты переработать опилки в продукт, который можно выгодно продать. И первый и самый очевидный вариант, который приходил на ум большинству, – это переработка в топливные брикеты, или пеллеты. К пеллетам относятся брикеты шнекового, ударного и гидравлического прессования. Но, проанализировав рынок, многие компании пришли к выводу, что цена на топливные брикеты сложилась настолько низкая, что получить большую рентабельность с такого производства было практически невозможно – ведь фактически по цене топливным брикетам приходится конкурировать с обычными дровами. К тому же для топливных брикетов нельзя использовать опилки большинства лиственных пород, с корой и лежалые.
Одним из рассматриваемых вариантов переработки опилок оказалось производство прессованных шашек для складских поддонов. И на удивление многих, в большинстве регионов России на этот продукт наблюдается многократное превышение спроса над предложением, ведь цена прессованной шашки из опилок ниже цены бруса, из которого изготавливают шашку большинство предприятий, а по потребительским свойствам прессованная шашка превосходит шашку из бруса – она не трескается, легче цельной древесины, не подлежит фитосанитарному контролю, у неё снята фаска ещё на этапе формовки, а благодаря полимеризации внешней грани она обладает отличной влагостойкостью. Рентабельность этого производства по расчётам оказалась на высоком уровне. И в данный момент довольно много компаний заходят в этот бизнес. Ведь для того чтобы оценить целесообразность организации данного производства в вашем регионе, достаточно осмотреться вокруг, нет ли поблизости деревообрабатывающего предприятия с кучей опилок.
Если такое предприятие есть, то с большой долей вероятности оно будет готово вам даже доплачивать за то, что вы будете вывозить эти опилки с их территории. Второе, что нужно сделать – это определить количество компаний в регионе, которые производят поддоны и которые заинтересованы в приобретении шашек. Если эти 2 фактора говорят о целесообразности такого бизнеса, то следует серьёзно рассмотреть возможность его организации, ведь данная ниша ещё не занята в большинстве городов РФ.
Расчёт
Сперва необходимо определиться, какой тип шашек мы будем производить. Возможно производство шашек для поддонов различного размера - сечением 100х100 - по ГОСТ 33757-2016, сечением 145х145 и 145х100 - такие применяются в европоддонах, а также варианты узкоспециализированных, облегчённых или удешевлённых поддонов - 100х80, 80х80, 120х120. Мы остановим свой выбор на размере 100х100 миллиметров, так как он самый распространённый.
На самом деле для расчётов тип шашек почти не имеет значения, т.к. цена этого продукта измеряется в рублях за кубический метр и не изменяется в зависимости от того, из каких шашек этот куб состоит. Но о том, какой тип шашек производить, следует задуматься до приобретения оборудования, так как один пресс может производить только один тип шашек, без возможности перенастройки или смены оснастки.
Исходные данные расчёта
- Комплект оборудования, который будет использоваться для производства шашек
Наименование | Количество, шт. | Производительность | Мощность, кВт | Цена, $ | Сумма, $ |
Дробилка YZ-37KW | 1 | 1000-3000 кг/час | 37 | 5 700 | 5 700 |
Сушилка барабанная 1X10 | 1 | 500 кг/час | 15 | 34 000 | 34 000 |
Смеситель JBJ-1000 | 1 | 1000 кг/час | 7,5 | 1 700 | 1 700 |
Пресс 9ST-6 | 2 | 0,6 м3/час | 65,2 | 15 000 | 30 000 |
- Дробилка роторно-молотковая YZ-37KW
Параметр | Значение |
Модель | YZ-37KW |
Мощность (кВт) | 37 |
Производительность (т/ч) | 2 - 3 |
Приемное окно (мм) | 250 х 250 |
Фракция на выходе (мм) | 3-7 |
Габариты (мм) | 1750 х 950 х 1100 |
Вес (кг) | 600 |
Цена ($) с НДС | 5700 |
Дробилка YZ-37KW относится к дробилкам гибридного типа – за ножами находится блок с молотками, которые обеспечивают измельчение сырья до размера, требуемого для производства шашки, за один проход. Дробилка взята с явным запасом по мощности по нескольким причинам. Первая – чтобы не возникало вопросов по тому, какое сырье она может переработать – практически любое, которое поместится в её приемное окно. Вторая – дробилка требует при себе постоянно находящегося работника, поэтому она должна работать как можно меньше, в идеале – один час в смену.
- Сушилка барабанная 1x10
Параметр | Значение |
Модель | 1x10 |
Производительность (т/ч) | 0,5 - 1,2 |
Диаметр барабана (м) | 1 |
Длина барабана (м) | 10 |
Расход твердого топлива (кг/ч) | До 200 |
Скорость вращения (об/мин) | 0,75 - 1,5 |
Мощность вращающего двигателя (кВт) | 5,5 |
Мощность циклона (кВт) | 15 |
Цена ($) с НДС | 34 500 |
Барабанная сушилка это надежный вариант для сушки опилок, со стабильной производительностью. Мы взяли барабанную сушилку, способную обеспечить сухим сырьем всю нашу линию, ведь для производства качественной шашки важна влажность. Оптимальная влажность опилок – около 8%.
- Смеситель центробежный JBJ-1000
Смеситель предназначен для смешивания опилок со связующим веществом. Разовая загрузка опилок – около 40 килограмм опилок на 7 килограмм клея. Рабочий цикл смесителя – 3 минуты, после которых опилки равномерно смешиваются и готовы к прессованию. Важно отметить, что не следует смешивать опилки сразу из сушилки – это может привести к застыванию смолы на этапе смешивания, опилкам необходимо остыть хотя бы в течение часа.
- Пресс для производства шашек для поддонов 9ST-6
Модель | 9ST-6 |
Количество фильер | 5 |
Размер бруса, опционально (мм) | От 65 до 120 |
Плотность бруса (т/м3) | 0,5-0,7 |
Габариты (мм) | 4800 х 580 х 1420 |
Вес (кг) | 1900 |
Мощность нагревательных элементов (кВт) | 24 |
Производительность (м3/сутки) | 4 - 8 |
Торцовочная пила | 4 - 8 |
Гидравлическая станция (кВт) | 5,5 |
Цена ($) с НДС | 15 000 |
Пресс – это основа линии для производства шашек. Используется горизонтальный гидравлический пресс с функцией нагрева фильер. Фильеры – это выходные отверстия пресса, их можно изготавливать сразу восьмигранной формы – со срезанными углами, - получая шашку со снятой фаской.
Мы берём самый большой пресс из имеющихся на рынке, поскольку он обеспечивает наилучшее соотношение цены к производительности. Пресс уже оборудован торцовочными пилами, поэтому мы сможем отрезать нужную нам длину и складировать получаемый брус на поддоны для последующей отправки клиентам.
Хочется отметить, что отверстие в центре бруса образуется нагревательным элементов в пуансоне пресса. Данный элемент обеспечивает более быстрый и равномерный прогрев шашки, а также облегчает её.
Мы выбрали данный комплект оборудования потому, что с помощью него можно обеспечить полный цикл переработки древесных отходов в прессованную шашку для поддонов. В качестве сырья может быть использован горбыль, ветки, щепа, опилки. В отдельную группу сырья можно выделить мебельные отходы – для них, как правило, не требуется сушка, что значительно снижает объём первоначальных инвестиций и упрощает процесс – этот вариант мы рассмотрим отдельно.
Интересно отметить, что линия подготовки сырья является универсальной и может быть использована с небольшими допущениями для производства топливных брикетов, пеллет, арболита. Для расчёта мы использовали линию полного цикла, и общая стоимость оборудования для нашего проекта составляет 4 284 0000 руб. Этой цифрой мы и воспользуемся для дальнейших расчётов.
Важный нюанс! Брус, выходящий из пресса, не может быть использован в строительстве – он обладает крайне низкой прочностью на излом, но отлично держит сдавливание, поэтому и используется в поддонах.
- Данные, необходимые для расчёта себестоимости продукции
Для производства шашки для поддонов необходимо всего 2 вида сырья - опилки и смола. Мы определились, что опилки и прочие древесные отходы будут нам доставаться бесплатно. А в качестве смолы возьмём очень распространенную марку КФМТ-15, её можно купить почти на любом лакокрасочном заводе, желательно ближайшем к вашему городу, чтобы не переплачивать за доставку. Средняя по России цена одной тонны смолы КФМТ-15 около 20 000 рублей. При покупке смолы также необходимо будет купить упаковку (еврокуб). Но эта тара оборачиваемая, и при следующих закупках её уже не нужно будет покупать. Далее в стоимость смолы закладываем 5000 рублей на доставку одной тонны от завода-производителя до нашего производства. Итого получается, что одна тонна смолы обойдётся нам в 30 000 рублей с учётом оборачиваемой тары. Считаем, что эта стоимость взята с запасом и в реальности может быть ниже. Но для расчётов возьмём пессимистичный прогноз цены сырья, чтобы в итоге получить финансовые показатели при не самых благоприятных рыночных условиях.
Расходы на электроэнергию, потребляемую указанным комплектом оборудования, составят 141 120 рублей в месяц. Затраты на зарплату сотрудникам, по нашим расчётам, составят 150 000 рублей в месяц. Мы взяли в расчёт два сотрудника в смену. Оборудование работает неспешно, выход бруса – около 10 сантиметров в минуту из каждой фильеры, двух человек достаточно для обслуживания всей линии. Для данного производства не потребуется оформление сертификатов, т.к. сертифицируются только целые складские поддоны, а шашки - нет.
Таким образом, общие затраты сырья на производство одного кубического метра шашек составят 2400 рублей, полная себестоимость одного куба шашек с учётом зарплаты, страховых взносов, амортизации и электроэнергии - 3460 рублей 46 копеек.
- Цифры, необходимые для расчёта плановой ежемесячной выручки
Прежде всего, нужно определиться по какой цене мы будем продавать один куб шашек. Для определения цены нужно будет провести мониторинг и учесть, что шашка конкурирует с брусом второй категории, хвойным, сухим, размером 100х100 миллиметров в сечении - именно такой брус используется для производства поддонов. Стоимость его в России разнится от региона к региону, мы встречали варианты от 8000 до 12 000 рублей. Для расчётов мы примем цену шашки как 7000 рублей - это позволяет ей конкурировать с брусом по цене и обеспечивает беспроблемный сбыт. Мониторинг показал, что обычно продажная цена шашки находится в промежутке от 7500 до 9000 рублей. Но в расчёт мы всё-таки заложим цену 7000 рублей за куб. Эта цена будет пессимистичным прогнозом. Производители шашек нам сообщили, что за такую цену можно очень быстро найти покупателей практически на любой объём продукции.
Далее нам необходимо рассчитать объём производства в сутки. Эту цифру мы легко получаем из производительности нашего оборудования. При восьмичасовой рабочей смене будет производиться 4,8 кубометров шашек. Т.е., работая в три смены в сутки, мы произведём 432 кубометра. И здесь следует сразу сделать примечание, почему выбран режим работы в 3 смены. Дело в том, что данная технология производства показывает высокую эффективность именно при круглосуточной работа станков. Это обусловлено тем, что каждый новый холодный пуск этого оборудования требует минимум 1 час на разогрев, настройку, чистку и прочее.
Теперь, зная наш месячный объём производства и помня, что одна из наших условностей гласит, что в расчётах мы всегда продаём всю продукцию, которую произвели, мы можем рассчитать нашу выручку за месяц. И она составляет 3 024 000 рублей.
Перед тем как приступить к расчёту финансового результата, следует сказать о сумме инвестиций в проект и из каких составляющих эта сумма состоит. Общая сумма, которую мы должны будем вложить в проект перед началом деятельности, составляет 7 827 840 рублей. Из них 4 284 000 рублей пойдёт на покупку оборудования. А оставшаяся сумма - это расходы на сырьё, электроэнергию и зарплату.
Показатели эффективности бизнеса за 3 года
Сумма инвестиций, руб. | 7 827 840,00 |
Выручка, руб. | 108 864 000,00 |
Балансовая прибыль, руб. | 55 046 880,00 |
Чистая прибыль, руб. | 34 863 024,00 |
Рентабельность продаж | 0,51 |
Срок окупаемости, мес. | 10,60 |
Рентабельность проекта | 4,45 |
Из полученных цифр можно сделать вывод, что, вложив в бизнес по производству шашек для поддонов 7,8 миллионов рублей, через 3 года мы получим 108,9 миллионов рублей оборота и 34,9 миллиона рублей чистой прибыли. Инвестиции в проект окупятся примерно за десять с половиной месяцев. Показатель рентабельности инвестиций равен 4,45.