Литьё алюминия под давлением – обзор технологии, актуальность производства, обзор оборудования
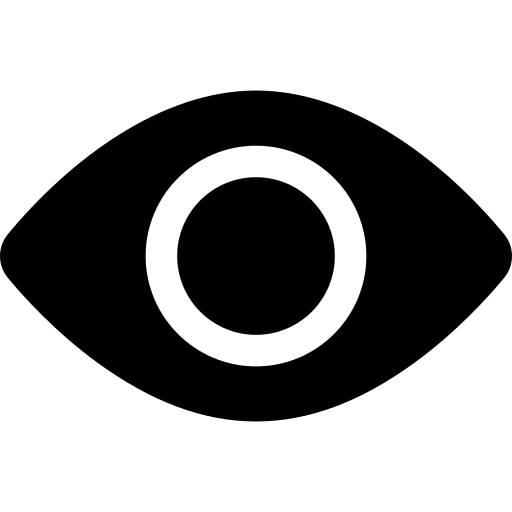
Детали из алюминия и его сплавов широко используются в ряде основных промышленных отраслей, таких как: машиностроение, приборостроение, авиастроение, судостроение и других. Благодаря своей превосходной теплопроводности и соотношению прочности к весу, этот металл является предпочтительным у многих разработчиков и производителей. Что касается методики литья алюминия под давлением, она хорошо известна с середины 20 века. Но только с 2000-х гг. появилась высокоточная технология. И за 20 лет с небольшим она снискала впечатляющее количество сторонников и продолжает заинтересовывать инженеров и производителей всего мира. Всё потому что гарантирует отсутствие усадки и отвечает высокому уровню точности при выполнении работ, не требует фрезерования и практически не оставляет отходов. Далее расскажем о технологии литья алюминия под давлением – MIM* и об актуальности этого производства, а также сделаем обзор оборудования.
*MIM – Metal Injection Molding, в буквальном переводе на русский «литье металла под давлением».
О технологии литья под давлением
Технология литья материалов под давлением появилась в конце 19 века. Тогда метод разработали для оловянно-свинцовых сплавов, из которых делали буквы газетопечатных машин (разработчиком стал Г. Брусс в 1838 г.). Затем способ MIM снискал применение для обработки керамики в начале 1940-х. В частности, из неё делали керамические бронебойные сердечники для снарядов. Для прочности керамику смешивали с карбидом, что придавало сердечнику высокую твёрдость. С металлом основательно начали работать в 1970-х. Пионером в области MIM стала американская компания Remington Arms – ведущий производитель военного и гражданского оружия в США. Это дало возможность изготавливать сложные и точные, и порой довольно крупные, части оружия, вплоть до пистолетного затвора.
Литье металлов под давлением в гражданских отраслях промышленности получило признание в 1990-х. К этому времени усовершенствовали сырьё и улучшили последующие процессы обработки. Конечное изделие работало так же или лучше, чем детали, изготовленные с помощью конкурирующих технологий: штамповка, литьё без давления, фрезеровка и других. Методика MIM повысила эффективность затрат за счёт больших объёмов производства на «чистой основе», исключив дополнительные дорогостоящие операции, такие как механическая обработка, резка и т.п. Хотя MIM считали слабой (некоторые считают и сейчас) с точки зрения строгих спецификаций размеров. Но и с этим недостатком научились справляться.
В 2002 году компания Advanced Materials Technologies (Сингапур) продемонстрировала высокоточную технологию литья под давлением. Разработчик успешно подверг экструзии алюминий и получил патент на именную методику «aluMIM». По словам представителей AMT, традиционные методы изготовления алюминиевых деталей, такие как литье и штамповка, – оставляют желать лучшего. Особенно когда речь идёт об их механических свойствах и свободе дизайна. Экструзия aluMIM даёт производителям такие же выгоды с экономической точки зрения, какие получили другие широко используемые технологии с металлами, керамикой и полимерами.
В целом литьё алюминия под давлением очень схоже с технологией экструзии деталей из пластика. Здесь также сырьё превращают в расплав, а затем загоняют в матрицу. После чего высвобождают заготовку и обрезают по краям.
Обзор технологии литья алюминия под давлением
Этапы MIM включают объединение металлических порошков с полимерами, такими как воск и связующие вещества полипропилена для производства «сырьевой» смеси Feedstock (международное обозначение гранулированной смеси, металлического порошка и связующих элементов). Расплав порошка, в жидкой фазе, вводят в форму с помощью поршня, установлено в узле машины для литья под давлением. Отформованная «зелёная» деталь охлаждается и выталкивается из матрицы. Затем часть связующего состава удаляют с помощью растворителей, термических печей, каталитических процессов или комбинации этих методов.
Полученная хрупкая и пористая заготовка, содержащая до 40% воздуха в объёме, находится в состоянии, называемом «коричневой» стадией. Далее ей требуется удаление связующих компонентов методом спекания. Детали MIM спекают при высоких температурах до 600°C, чтобы вызвать частичное плавление в процессе, называемом спеканием в жидкой фазе. Скорость диффузии высока, что приводит к усадке и уплотнению. Если это делается в вакууме, то обычно достигается плотность твёрдого вещества до 99%.
Металл конечного продукта приобретает механические и физические свойства, сравнимые с деталями, изготовленными классическими методами. Дальнейшая термическая обработка после спекания для MIM аналогична другим производственным процессам для металлов.
Высокоплотный материал прекрасно поддаётся таким стадиям, как:
- отжиг;
- пассивация;
- науглероживание;
- гальваническое покрытие;
- азотирование и дисперсионное твердение.
Готовые детали MIM не уступают металлическим аналогам, полученным конкурентными способами. Поэтому используются в широком спектре промышленных, коммерческих, медицинских, стоматологических, оружейных, аэрокосмических и автомобильных производственных отраслей.
Схема производства – пошагово
Первый этап: подготовка фидстока
Приготовление смесей Feedstock, применяемых в литье под давлением, проходит на оборудовании при использовании утверждённых технологий. В конечном итоге получаются гранулы одинакового размера и гомогенного по составу.
Второй этап: экструзия фидстока
MIM детали изготавливаются на пресс-машинах. Материал впрыскивается в матрицы, учитывающие усадку материала. Полученные заготовки пока имеют низкий уровень прочности и поэтому называются «зелёными».
Третий этап: химическое удаление присадок
В специальной установке удаляются присадки из «зелёной» детали посредством химических реакций. Такой процесс способствует открытию капилляров в заготовке. Во время данного процесса связующие элементы могут диффундировать или улетучиться.
Четвёртый этап: термическое удаление присадок
Оставшиеся присадки в детали после химической обработки удаляются термическим способом. Во время термической обработки, большая часть связующих элементов сгорает в печи при температурах 200–600 °C в защитной атмосфере. После такой процедуры прежние заготовки зелёного цвета становятся коричневыми и очень хрупкими.
Пятый этап: спекание
В высоковакуумной печи коричневые детали доводятся до температуры синтеза. Металлический порошок сплавляется, поры исчезают и деталь приобретает необходимую плотность. Происходит усадка в необходимые, просчитанные заранее размеры. Такая технология производства позволяет достигать плотности МIМ-продукции до 99%, в сравнении с катаными изделиями.
Шестой этап: обработка продукта
В зависимости от свойств и сложности будущей детали, её калибруют механическим способом, иногда на станке, что позволяет соблюсти жёсткие допуски и корректировать отклонения.
Дозволяются припуски ± 0,3%, а для более жёстких допусков применяется механическая обработка. Благодаря технологии MIM можно производить такие детали, где сложно или даже невозможно эффективно изготовить конструкционные элементы с помощью других производственных методов.
Преимущества и недостатки литья алюминия под давлением
Как и любая технология, MIM не лишена своих положительных и отрицательных характеристик. О них важно знать, если рассматривать метод литья алюминия под давлением в качестве организации бизнеса.
Преимущества:
- MIM обеспечивает изготовление мелкоразмерных деталей в больших объёмах.
- Позволяет свободно изготавливать сложные формы, стоимость которых при использовании других методов считалась бы непомерно высокой.
- Можно добиться уникальности сложных форм, среди которых: внутренняя и внешняя резьба, профилированные отверстия и мелко детализированная текстура поверхности, накатка, гравировка и маркировка.
Недостатки:
- Более высокая стоимость запуска проекта, поскольку требуются большие первоначальные инвестиции на производственное оборудование.
- Ограничение размера деталей, поэтому MIM очень хорош для небольших изделий и не подходит для выпуска продукции более 20 см.
- Серийность: технология MIM годится исключительно для больших тиражей продукции.
Ещё к преимуществам можно добавить возможность объединения нескольких операций в один процесс, что гарантирует экономию средств и времени на выполнение заказов, и даёт производителям значительные преимущества перед конкурентами. К тому же процесс литья под давлением считается экологически чистой технологией из-за значительного сокращения отходов по сравнению с «традиционными» методами производства, такими как 5-осевая обработка на станке с ЧПУ. А это ещё один плюс.
Основные преимущества литья под давлением (высокая производительность, точность размеров отливки и высокое качество поверхности) в полной мере могут быть реализованы только в том случае, если при конструировании литой детали учтены все особенности технологического процесса.
Актуальность производства по литью алюминия под давлением
Способ литья алюминия под давлением позволяет выпускать простые и сложные по конфигурации заготовки, как из чистого гранулированного порошка, так и смесей с добавлением: меди, магния, цинка, кремния, кобальта, хрома, вольфрама и других. Продукция широко востребована, и по отзывам действующих MIM-компаний среди заказчиков встречаются:
- Военная промышленность (корпуса турбин, крыльчатки, крышки, кронштейны, корпусное литье);
- Электротехническая промышленность (кронштейны, распорки, корпуса);
- Автомобильная промышленность (фланцы, кронштейны, шарниры);
- Приборостроение (отливки корпусов, визиров, шнеков, качелек).
- Народный потребитель (втулки, барабаны, разделители).
Перечень заказчиков и клиентов далеко не полный. Ведь почти в каждой отрасли есть механизмы с алюминиевыми деталями. Они изнашиваются или ломаются, поэтому требуют замены (те же крыльчатки и фланцы). Всё это говорит об актуальности цеха по литью алюминия под давлением. Но есть конкуренция.
Угроза конкуренции исходит не столько от отечественных производителей, сколько извне. За последние 10-15 лет наш рынок экспансировали китайские, индийские и ближневосточные компании. Не удивительно, ведь рост потребления алюминия в РФ происходит на фоне активной урбанизации и индустриализации. Аналогичная ситуация во всём мире. Например, в 2012 г. глобальный рынок MIM-технологий составлял $1,51 млрд, а в 2017 г. его оценивали в $2,88 млрд. Чуть меньшая динамика роста ожидается в пятилетку 2018-2022 г. Отчёт появится в 2023-м (источник: Skolkovo Ventures). Географически рынок MIM локализован следующим образом:
- 47% – страны Азии;
- 26% – Северная Америка;
- 21% – Европейские государства;
- 6% – остальные страны.
Лидеры MIM-рынка:
- Taurus (Бразилия).
- Ecrimesa (Испания).
- Indo-US MIM (Индия).
- Epson Atmix Corp. (Япония).
- Schunk Sintermetalltechnik (Германия).
- Changzhou GIAN Technology Co. Ltd.; Zhejiang Yihuo Tech Co., Ltd. (Китай).
- ARC Group, Parmatech Corp.; Kinetics Climax, Inc.; Smith Metal Products; Dynacast (США).
- Acelent Technologies Pte Ltd.; Advanced Materials Technologies Pte Ltd.; SolidMicron Technologies Pte Ltd. (Сингапур).
Несмотря на то, что одним из крупнейших производителей алюминия в мире является российская компания РУСАЛ, в нашей стране плохо развита отрасль литья под давлением. Поэтому отечественным предпринимателям есть куда стремиться. Тем боле государство обещает отдавать предпочтение местной продукции, следуя курсом импортозамещения. А гранулированное алюминиевое сырье в достаточных количествах выпускают российские комбинаты. Всё перечисленное является ещё одним объективным критерием в портфеле актуальности производства MIM-деталей.
Обзор оборудования
Предлагаем небольшой обзор 3-х машин для литья алюминия под давлением, с кратким описанием и основными характеристиками.
Горизонтальный пресс для экструзии алюминия HJT-1200T
Машина серийного производства алюминиевых профилей для дверных и оконных систем. Технология экструзии с прессованием обеспечивают непрерывный процесс производства сотен и тысяч метров продукции. Алюминиевые детали выходят из матрицы и перемещается на «выводной» стол. Затем охлаждаются на «растяжном» столе и разрезаются на куски для транспортировки. Управление операциями происходит при помощи программируемого логического контроллера.
Модель | HJT-1200T |
Диаметр стержня (мм) | Φ152 |
Величина хода поршня (мм) | 350 – 650 |
Режим работы | Автоматический / ручной однотактный |
Размер выходной фильеры (мм) | Φ180 х 250 |
Номинальное усилие экструзии кН | 1200 |
Номинальное давление в системе, (МПа) | 24 |
Напряжение (В) | 380 ± 10% |
Скорость экструзии, (мм/с) | 0,3 – 13,3 мм/с (регулируемая) |
Главный масляный насос (шт) | A15V280 (2 комплекта серии Rexroth) |
Вспомогательный масляный насос (шт) | 4525V60A17 (1 комплект серии Vickers) |
Мощность главного двигателя (кВт) | 110 / 6 полюсов |
Мощность блокирующего двигателя (кВт) | 5,5 / 6 полюсов (1 комплект, Луань, Аньхой) |
Система управления | PLC FX3U-128MR (Mitsubishi, Япония) |
Сенсорный экран | Kunlun Tongshi |
Контакторы, реле, кнопочные переключатели | Schneider |
Размеры основания штампа (фильеры) (мм) | Φ300 × 300 |
Высота центров машины (мм) | 1150 |
Габаритные размеры (мм) | 11000 х 4000 х 4000 |
Вес (кг) | 35000 |
Литейная машина для литья под давлением с холодной камерой прессования FORTECH-PAK DCC900
Литейная машина для литья под давлением с холодной камерой прессования предназначена для эксплуатации на крупных металлообрабатывающих предприятиях. Применяется для работы с алюминиевыми сплавами, латунью, медью и магнием с целью получения деталей путём заполнения пресс-форм под давлением с высокой скоростью. Машины подходят для широкого диапазона литья, поскольку предусмотрена замена пресс-форм.
Модель оснащена:
- системой заливки металла с клапанами большого диаметра;
- высокопроизводительным сдвоенным насосом;
- двухскоростным подвижным поршнем;
- двойным контуром с аккумуляторами;
- планетарным зубчатым механизмом;
- системой централизованной смазки;
- точным всасывающим фильтром;
- гидравлическим эжектором.
Модель оборудована системой автоматического управления на базе цифровых технологий. Контроль данных, их запись и сохранение в памяти компьютера, позволяют анализировать графики впрыска и дублировать производственные алгоритмы без повторного ввода: параметров давления, скорости и перемещения. Компьютер наделён функциями диагностики неисправностей.
Модель | DCC900 |
Усилия запирания (кН) | 9000 |
Ход подвижной плиты механизма запирания (мм) | 800 |
Толщина пресс формы (мин - макс) (мм) | 400-1000 |
Размер шаблона (по горизонтали/вертикали) (мм) | 1460×1460 |
Максимальный вес отливки (кг) | 9.1 |
Площадь литья (см²) | 795 |
Габаритные размеры (мм) | 8300×3800×3625 |
Литейная машина для литья под давлением с горячей камерой прессования CLASSIC-PAK-III DC30
Литейная машина для литья под давлением с горячей камерой прессования. Представляет собой электромеханическое устройство, предназначенное для эксплуатации на крупных металлургических предприятиях для изготовления изделий из алюминиевых сплавов с цинком и магнием. Конструкция модели состоит из таких систем и узлов, как:
- Газовая печь.
- Главный электродвигатель.
- Система водяного охлаждения масла.
- Центральные и внешние пары направляющих.
- Автоматическая централизованная система смазки.
- Гидравлическая система (запирающий узел, составной эжектор).
- Автоматическая масляная горелка с высоким и низким давлением впрыска.
- Электронагревательный элемент для подогрева и поддержания постоянного уровня температуры сопла и змеевика.
- Система подачи и впрыска расплава (две стадии), в состав которой входит: змеевик, сопло, ванна, аккумулятор поршневого типа.
Машина оснащается системой автоматического управления с кнопочным пультом и сенсорным экраном. Программируемый контроллер выполняет функции диагностики ошибок работы, записи параметров применяемых ранее пресс-форм и иных первичных параметров.
Модель | DC30 | |
Усилие запирания (кН) | 300 | |
Ход подвижной плиты механизма запирания (мм) | 180 | |
Толщина пресс-формы (мин - макс) (мм) | 100–310 | |
Размер шаблона (по горизонтали/вертикали) (мм) | 407×393 | |
Сила давления поршня, (кН) | 40 | |
Рабочее давление системы (мПа) | 8 | |
Мощность двигателя (кВт) | 7,5 | |
Ёмкость гидробака (л) | 200 | |
Отогрев сопла отлива, (кВт) | 1,5 | |
Потребление энергии | Электрическая печь (кВт) | 26 |
Дизельная печь (кг/час) | 3.5 | |
Габаритные размеры (мм) | 3550×1430×1830 | |
Вес (кг) | 2600 |
Представленное в обзоре оборудование изготавливается в Китае, сертифицируется и поставляется в РФ для продажи. Отличается хорошим качеством и длительным сроком службы (не менее 10 лет).
Заключение
Литьё алюминия под давлением – интересная и актуальная ниша для отечественной промышленности. Выпускаемая продукция широко востребована, а технология производства несложная. К тому же рынок предлагает развёрнутый ассортимент оборудования с автоматикой, а сырьевая база – гранулированный алюминий, оксиды и смеси – всегда есть в наличии у оптовиков и производится на комбинатах РФ в достаточных количествах.