Лазерные технологии в станках – виды, особенности, области применения
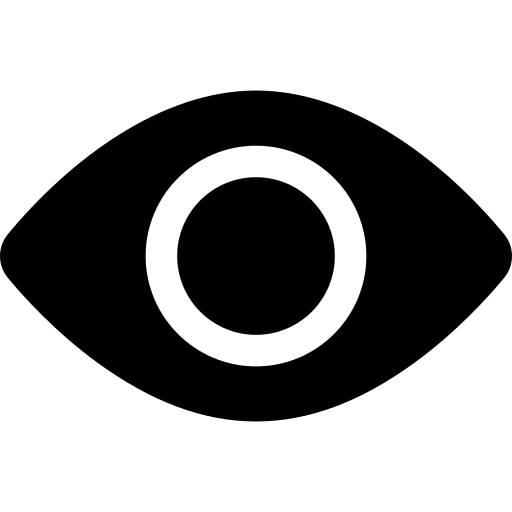
Сегодня лазер является широко используемым инструментом в промышленности. Кругом внедряется аддитивное производство, а мировая экспансия Индустрии 4.0 позволяет инженерам разрабатывать сложные продукты с жёсткими допусками конструкций. И здесь благодаря появлению лучевой технологии можно выполнять настолько тонкую обработку, которую трудно или невозможно было бы совершать с помощью традиционного обрабатывающего оборудования. Например, после лазерной резки мы получаем сверхчистый срез, без заусенцев или теплового воздействия на граничную область материала, что освобождает от необходимости вторичных этапов чистовой обработки.
Лазерные технологии снискали популярность в производстве высокоточного медицинского оборудования, поскольку позволяют обрабатывать мелкие и совершенные продукты. А кроме этого их применяют теперь в сварочных аппаратах на автомобильных заводах (Volvo Cars, Nissan, Toyota, Hyundai, General Motors, Ford Motor Company, DaimlerChrysler, BMW, Volkswagen, Audi), в судостроении (технология LaserHybrid), в гравировальных и маркировочных машинах, в перфорированных станках и т.п. Но лазеры бывают разными и для различных задач. Поэтому далее мы расскажем о видах, особенностях и областях применения этого инструмента.
Что такое лазер?
Лазер (англ. laser, абревиация от Light Amplification by Stimulated Emission of Radiation – «усиление света с помощью вынужденного излучения») – квантовый генератор, излучающий пучок когерентного света в процессе оптического усиления. Излучение может быть:
- непрерывным с постоянной мощностью;
- импульсным, достигающим предельно больших пиковых мощностей.
Существует несколько типов лазеров: газовые (СО2-лазеры), волоконные (CW-лазеры), твердотельные (Nd-лазеры), струйные (на красителях), диодные и эксимерные. Наибольшее распространение в промышленных станках получили первые 3 вида. Но все перечисленные типы излучателей имеют общий базовый набор из 3-х компонентов:
- Активная (рабочая) среда.
- Источник энергии (накачки).
- Резонансная полость (оптический резонатор).
Первый пункт включает в себя активное вещество, которое может быть: твёрдым, жидким и газообразным. Второй – электрический ток, импульсная лампа или химическая реакция. А третий – пару параллельных друг другу зеркал, между которыми помещается активная среда.
История лазерной технологии
Основа лазерной технологии появилась 1916 году благодаря мыслительным процессам Альберта Эйнштейна (1879-1955). Будучи увлечённым неоновой лампой, которую в 1910 г изобрёл французский химик Жорж Клод (1870-1930), он спрогнозировал явление «стимулированного излучения». Для этого Эйнштейн добавил к лампе два зеркала, в результате получился луч. Журналисты сразу прозвали изобретение «луч смерти». Оно и стало основой работы всех лазеров.
Дальнейшее развитие по горячим следам технология не получила. И только в 1960-м он ней снова вспомнили. Тогда в исследовательских лабораториях Хьюза были закончены работы над самым первым оптическим квантовым генератором на искусственном кристалле рубина. Разработчиком аппарата стал американский физик Теодор Майман (1927-2007). После демонстрации изобретения инженеры и физики всего мира включились в гонку по созданию всевозможных лазеров, которая продолжается по сей день.
Лазерная технология в обработке материалов
Энергия луча используется для изменения формы или внешнего вида любого материала. К тому же этот метод даёт широкий ряд преимуществ, по сравнению с традиционными технологиями обработки. Среди достоинств можно выделить основные:
- Бесконтактное воздействие на обрабатываемую поверхность.
- Высочайшее качество раскроя, реза, выжигания, сварки.
- Изготовление сложных форм.
- Высокая скорость операций.
- Не требуется обработка.
Ещё одним преимуществом лазерной технологии является способность обрабатывать многообразие материалов. Среди них:
- неметаллы: камень, дерево, керамика, композиты, пластмассы/полимеры, клеи и др.;
- металлы: железо, алюминий, медь, нержавеющая сталь, титан и др.
Всё перечисленное замыкает экономическая эффективность. Поскольку лазерные станки снижают затраты на производство небольших партий деталей. Например, в некоторых случаях отсутствует необходимость в изготовлении или приобретении форм для прессования, ковки или литья, а вместите с этим отпадает надобность в ряде технологических процессов.
О взаимодействии с материалами
Эффекты, вызываемые лазерной энергией, сильно зависят от длины волны и уровня мощности лазера, а также характеристик поглощения и химического состава материала. Обычными длинами волн для лазерной обработки являются:
- 10,6 микрона у CO2–лазеров;
- 1,06 микрона у волоконных и твердотельных излучателей.
Для каждого типа квантового генератора предусмотрен диапазон уровней мощности, что оптимизирует взаимодействие энергии луча с материалом. В одних случаях требуется высокая мощность – для резки или сварки, а в других малая – для выжигания поверхностного слоя. Поэтому характеристики поглощения и химический состав материала, а также желаемые результаты, сильно влияют на выбор типа лазера и уровня мощности. Эффект взаимодействия усиленного света с обрабатываемой заготовкой называют абляцией.
Абляция (лат. ablatio – удаление) – это удаление или разрушение чего-либо с поверхности объекта путём испарения, сколов, эрозионных процессов или другими способами.
Виды абляции в лазерных станках
Во всех лазерных процессах на станках энергия усиленного луча взаимодействует с материалом, тем или иным образом трансформируя его структуру. Каждое такое преобразование, в определённом процессе, контролируется путём точного регулирования:
- мощности;
- длины волны;
- рабочего цикла и частоты повторения.
В зависимости от технического оснащения станка и настроек, лучевая технология способна выполнять следующие процессы:
Лазерная резка
Сквозное испарение материала по чёткому пути, заданному программным обеспечением машины в рамках цифрового G-кода. В самом узком месте лазерный луч, обычно, имеет диаметр менее 0,32 мм, но возможна ширина разреза до 0,10 мм, в зависимости от толщины материала.
Лазерная сварка
Термический способ соединения деталей, осуществляемый плавлением под воздействием тепловой энергии лазерного луча, уже не редкость. Технология является универсальной, поскольку определяет широкий спектр материалов для сваривания, среди которых:
- Стали: углеродистые; низколегированные; высокопрочные; нержавеющие.
- Сплавы: алюминия; меди; бронзы; латуни; титана; цинка; хрома; никеля.
- Стекло: кварцевое; натриево-силикатное; известковое; свинцовое.
- Пластики: термопласты; реактопласты; эластомеры.
- Драгоценные металлы: золото; серебро; платина.
Сварка лазерным лучом отличается высокой плотностью энергии в пятне контакта. Поэтому разогрев и охлаждение шва происходят очень быстро. Вдобавок околошовная зона нагревается слабо, что никак не нарушает свойства материала (речь об отсутствии разупрочнения). Подробнее о лазерной сварке мы писали в статье «Лазерная сварка: Технология. Области применения. Виды оборудования», опубликованной на другом нашем сайте.
Лазерное сверление (перфорирование)
Точечное удаление материала – метод прокалывания – при котором импульсный лазер высокой мощности быстро делает отверстие.
Для справки: на прокол 13-миллиметрового листа из нержавеющей стали лазеру потребуется 5 – 15 секунд.
Лазерная гравировка/травление/очистка
Удаление верхнего слоя с поверхности материала на заданную глубину. Например, такая технология сегодня часто встречается на аппаратах по удалению ржавчины.
Лазерная маркировка
Клеймение поверхности материалов для создания удобочитаемых человеком и/или машинами буквенно-цифровых символов, одномерных/двухмерных штрих-кодов, логотипов, знаков отличия и т. д., – главным образом применяется с целью идентификации. Уникальность лазерной технологии здесь в том, что рабочая длина волны электромагнитного излучения, от 510 до 10 600 нанометров (0.51 до 10.6 микрон), – определяет широкую группу кодируемых материалов, таких как:
- Кожа.
- Стекло.
- Резина.
- Картон.
- Камень.
- Металл.
- Древесина.
- Микроэлектроника.
- Полимеры и другие.
При этом тепловое воздействие лазера нисколько не меняет свойства маркируемой продукции.
Лазерный отжиг
Энергия луча нагревает материал непосредственно в точке фокусирования, вызывая фазовое изменение (например, из аморфного состояния в поликристаллическое).
Лазерная гравировка (фотогравировка)
Бесконтактный перенос рисунка, надписи или орнамента на поверхности: металла, камня, дерева, пластика или стекла, – лучевым способом. Формат работы может быть: двухмерным (2D) или трёхмерным (3D). Последний делится на 2 вида:
- поверхностный;
- глубокий.
Поверхностный формат достигает глубины выжигания не более 50 микрон; глубокий – от 50 до 1 000 микрон и более (1 мкм = 0,001 мм).
Лазерная обработка
Контролируемое удаление материала с помощью комбинации лазерной резки, гравировки, перфорации, – для создания определённой формы, размера или внешнего вида изделия.
Обзор 5-и лазерных технологий
Многообразие лазеров определяется их назначением и возможностями. Наиболее популярными в лёгкой и тяжёлой промышленностях сегодня считаются 5 видов излучателей, таких как:
- Газовые СО2-лазеры.
- Твердотельные Nd:YAG-лазеры.
- Волоконные QCW/CW-лазеры.
- Жидкостные (лазеры на красителях).
- Полупроводниковые (лазерные диоды).
Главное различие у перечисленных типов в способе накачки. Накачкой могут служить: электрический ток; пучок релятивистских электронов; электрический разряд; электромагнитное излучение с длиной волны, отличающейся от лазерной; химическая реакция в пригодной для генерации среде.
Газовые лазеры
Промышленный излучатель, в котором электрический ток проходит через газ или смесь паров для генерации света посредством процесса, известного как инверсия электронных населённостей. Этот вид генераторов образует целую группу излучателей, в которую входят такие газовые лазеры, как:
- углекислотные (CO2);
- гелий-неоновые;
- криптоновые;
- эксимерные;
- аргоновые.
Используются они в самых разных промышленных областях, включая голографию, спектроскопию, сканирование штрих-кодов, измерение загрязнения воздуха, лазерную хирургию и обработку материалов (резка, перфорация, гравировка и сварка).
В целом CO2-лазеры являются самыми мощными представителями лучевой технологии, поэтому их часто используют в тяжёлой промышленности. Например, для сварки материалов любой сложности и толщины (сталь до 2 см).
Твердотельные лазеры
Твердотельные (неодимовые) Nd:YAG-лазеры в качестве источника оптического усиления используется натуральное или искусственное твёрдое тело (кристаллы или стекла) с ионами группы железа Fe (неодима, хрома, эрбия, тулия, иттербия) или ионами редкоземельных элементов. Наиболее известным твердотельным видом является рубиновый лазер, так как это первый из когда-либо созданных квантовых излучателей.
Лазер Nd: YAG (алюминиевый гранат, легированный неодимом) широко используется в станках для обработки материалов. А кроме этого он встречается в медицинских и косметических аппаратах по удалению татуировок, волос, абляции родинок, живых тканей и камней в почках. Помимо сказанного, технология твердотельного излучения Nd:YAG сегодня всё чаще находит применение в гибридной лазерной сварке – LaserHybrid. В частности, она снискала популярность на судовых верфях для сварки тонких листов с высокой скоростью.
Таблица 1: Сравнение технологии сварки Laser-Hybrid с другими технологиями
Характеристики / Технология | Дуговая сварка под флюсом | LaserHybrid | Лазерная сварка с присадочной проволокой |
Скорость (%) | 100 | 300 | 150 |
Толщина (мм) | <12 | <15 | <15 |
Зазор (мм) | 2 – 5 | 0 – 1 | 0 – 0,4 |
Деформация (мм/м) | <1,5 | <0,2 | <0,1 |
Металлургия | некритично | некритично | критично |
Усталостные свойства | хорошие | отличные | критично |
Волоконные лазеры
Волоконный QCW/CW- лазер — это дальний родственник твердотельного лазера, который образует отдельную категорию излучателей. Здесь усиливающей средой является оптическое волокно (кремнеземное стекло), смешанное с редкоземельным элементом. Лазерный луч волоконного генератора более прямой и миниатюрный, чем у других аналогов, что делает его гораздо точнее. Также волоконные лазеры известны:
- компактностью;
- хорошим электрическим КПД;
- низкими затратами на техническое обслуживание и эксплуатацию.
Применяются в ряде промышленных отраслей, включая заводскую обработку материалов (очистка, текстурирование, резка, сварка, маркировка), медицину и электронную индустрию. Наиболее часто встречаются в продаже иттербиевые (IPG) и легированные эрбием (Er:YAG) волоконные лазеры.
Жидкостные лазеры (лазеры на красителях)
В жидкостных лазерах в качестве усиливающей среды используется органический краситель в жидкой форме. Они также известны как лазеры на красителях. Используются в медицине, спектроскопии, удалении родимых пятен и разделении изотопов. Одним из преимуществ лазеров на красителях является возможность генерировать гораздо более широкий диапазон длин волн. Это делает их хорошими кандидатами на роль перестраиваемых лазеров, где длину волны можно контролировать во время работы.
Полупроводниковые лазеры (лазерные диоды)
Лазерные диоды (полупроводниковые лазеры) похожи на обычные диоды тем, что они имеют положительно-отрицательно заряженный переход (полярность). Отличие состоит лишь в слое на PN-переходе из материалов, создающих спонтанное излучение. Внутренний слой отполирован так, что генерируемые фотоны усиливаются, преобразуя электрический ток в лазерный свет.
При том, что большинство полупроводниковых лазеров являются диодными, некоторые из них таковыми не являются. Это связано с той особенностью, что существуют полупроводниковые лазеры без диодной структуры. Среди них: квантовые каскадные лазеры и полупроводниковые лазеры с оптической накачкой.
Как и волоконные излучатели, диодные могут быть классифицированы как твердотельные, поскольку их активная среда является твёрдой. Однако они относятся к отдельной категории из-за своего соединения PN. В целом диодные лазеры чрезвычайно распространены. Они используются в считывателях штрих-кодов, указках, принтерах, сканерах и ряде других изделиях.
Режимы работы лазеров
Все типы лазеров, перечисленные выше, в зависимости от конструкции могут работать в одном из двух режимах: импульсном или непрерывном. В генераторах с непрерывным излучением существует постоянный поток энергии, что означает непрерывную передачу усиленного света. Наиболее распространённым примером является непрерывный луч лазерной указки. Такой метод обычно используются для лазерной резки и лазерной сварки.
В импульсных лазерах луч прерывается через равные промежутки времени, чтобы позволить энергии накапливаться и достигать более высокой пиковой мощности, чем у излучателей непрерывного действия. Усиленный свет испускается в виде импульсов, которые имеют определённую длительность импульса*. Такая высокая плотность энергии требуется во многих рабочих процессах, таких как точечная сварка и гравировка.
*Длительность импульсов (Δt, с) – время, в течение которого мгновенная мощность лазерного излучения превышает значение, соответствующее уровню 0,5.
При выборе лазеров имейте ввиду, что модели непрерывного действия могут показаться более мощными, чем импульсные, потому что их заявленная мощность обычно намного выше. Это может ввести в заблуждение. Дело в том, что в названии станка с импульсным лазером часто указывается средняя мощность луча, а средняя мощность импульсных лазеров обычно ниже, даже если они достигают более высоких мощностей на пике.
Например, лазер непрерывного действия мощностью 6000 Вт непрерывно излучает 6000 Вт лазерной мощности. И наоборот, импульсный лазер мощностью 100 Вт может испускать импульсы мощностью 10 000 Вт каждый.