Закалка метизов – технология, выбор оборудования, успешные кейсы
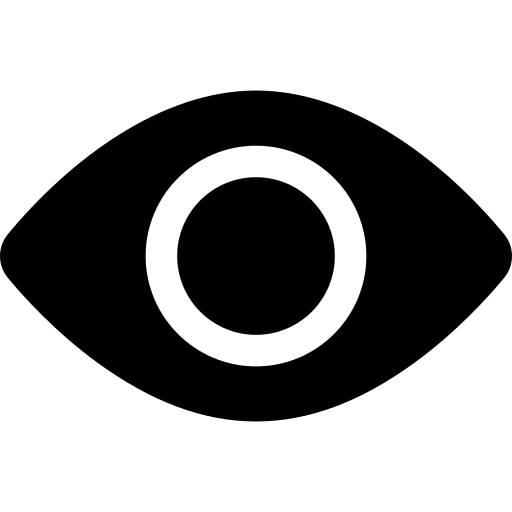
Закалка металлических изделий, таких как саморезы, болты, гайки, гроверы, пружины, шпильки, анкеры и другие, наделяет их прочностью и долговечностью. В условиях современного производства, где требования к качеству крепёжной продукции постоянно растут, необходимость в первоклассной закалке становится всё более актуальной. Однако, несмотря на очевидные преимущества термической обработки, многие предприятия сталкиваются с проблемой выбора закалочного оборудования из-за разнообразия его видов. Рынок предлагает изотермические, индукционные, лазерные, криогенные и другие виды камер. Возникает вопрос: в какую из них инвестировать?
Зачем закаливают метизы
Закаливание металлических изделий практикуется издревле. Согласно исследованиям, люди занимались термической обработкой стальных инструментов ещё 3000 лет тому назад. Тогда и сейчас технология позволяет значительно повысить механические свойства металла, такие как:
- Твёрдость,
- Прочность,
- Износостойкость.
В условиях эксплуатации, где конструкции подвергаются высоким нагрузкам, закалённые детали являются обязательными, чтобы предотвратить деформации и разрушения. Такие высокопрочные метизы могут выдерживать высокие температуры, поэтому используются в узлах и агрегатах, подверженных тепловым нагрузкам (в частности, болты, шайбы и гайки). Увеличивается срок их службы, снижая необходимость в частой замене и ремонте.
В каких сферах используют закалённые метизы (основные потребители)
Высокопрочные метизы находят применение в самых разных отраслях промышленности благодаря своей повышенной износостойкости и устойчивости к механическим нагрузкам. Вот несколько ключевых сфер их использования:
1. Строительство
Закалённые крепежи широко применяются при возведении зданий и сооружений, особенно там, где требуется стабильная надёжность соединений.
Например:
- анкеры для крепления конструкций к бетонным основаниям,
- саморезы и шурупы для монтажа деревянных каркасов,
- болты и гайки для сборки металлоконструкций.
2. Автомобилестроение
В автомобилестроении закалённые метизы используется для повышения долговечности узлов и агрегатов, работающих под высокой нагрузкой:
- элементы подвески и рулевого управления,
- крепежи для двигателя и трансмиссии,
- соединительные элементы кузова.
3. Станкостроение
Метизы, прошедшие закалку, востребованы в производстве обрабатывающих машин, станков и другого промышленного оборудования:
- гайки и шпильки для крепления тяжёлых узлов,
- винты и болты для сборки станков и механизмов,
- штифты и оси для подвижных частей механизмов.
4. Энергетика
В энергетике, особенно в строительстве электростанций и линий электропередачи, довольно часто используются высокопрочные метизы.
С их помощью собирают:
- высоковольтные опоры и мачты,
- устройства заземления и молниезащиты,
- крепёжные элементы для трансформаторов и генераторов.
5. Железнодорожный транспорт
Железные дороги и подвижной состав требуют особо прочных крепёжных конструкций, чтобы выдерживать большие нагрузки и вибрации:
- крепление элементов вагонов и локомотивов,
- заклёпки и болты для рельсовых путей,
- узлы сцепок и тормозной системы.
6. Авиакосмическая отрасль
Здесь требуются максимально надёжные соединения, так как конструкционные ошибки могут привести к катастрофическим последствиям. Поэтому высокопрочные метизы используются для:
- сборки корпусов самолётов и ракет,
- фиксации двигателей и топливных систем,
- монтажа авиационных приборов и электроники.
7. Судостроение
Корабли и суда испытывают значительные механические воздействия от волн и солёной воды, поэтому судостроители используют прочные метизы. Они применяются в таких областях конструкций, как:
- механизмы подъёмных устройств и якорей,
- крепления палубного оборудования,
- системы крепления корпуса судна.
8. Военная техника
Для военной техники также необходимы особо прочные крепежи, способные выдержать экстремальные условия эксплуатации. Закалённые метизы нужны в таких видах вооружения, как:
- авиация и ракеты,
- вооружение и бронированные машины,
- подвижные механизмы танков и бронетранспортёров.
9. Горнодобывающая промышленность
Работа в шахтах и карьерах требует максимальной надёжности всех компонентов оборудования, таких как:
- детали конвейеров и дробилок,
- крепёжные элементы бурильных установок,
- болты и гайки для экскаваторов и погрузчиков.
10. Медицинская техника
Даже в здравоохранении применяются закалённые метизы, когда речь идёт о надёжном креплении медицинских аппаратов или высокопрочных инструментах.
Среди них:
- хирургические скальпели и зажимы,
- медицинские кровати и операционные столы,
- компоненты рентгеновского и ультразвукового оборудования.
Перечисленные сферы подчёркивают важность закалённых метизов в современных технологиях и производственных процессах, где требуются высокие эксплуатационные характеристики. Следовательно, круг потребителей продукции очень широкий.
Перспективы отрасли
Эксперты аналитического агентства в области металлургии Rusmet утверждают, что спрос на закалённые металлические изделия в России стабильно растёт. Например, в 2020 г. отечественными компаниями было произведено около 70 тыс. т высокопрочного крепежа (болты, гайки, шайбы), что более чем в 1,7 раза превышает уровень 2010 г. Растущая тенденция сохранится на следующие 10 лет (2020-2030 гг.), что выглядит весьма многообещающим для компаний-изготовителей.
Такая востребованность обусловлена повышающимися требованиями к прочности и производительности метизов в различных секторах промышленности. Тем более сейчас, когда Россия активно развивает свои мощности, особенно в таких отраслях, как:
- авиастроение,
- машиностроение,
- судостроение и энергетика.
Внедрение новых технологий закаливания (лазерное, плазменное, криогенное и другие современные методы) позволяет улучшить качество и характеристики металлических изделий, а также снизить затраты на производство.
Программы государственной поддержки и инвестиции в научные исследования и разработки способствуют развитию технологий закаливания и увеличению производства высококачественных метизов.
Рост объёмов продукции с одновременным улучшением её качества может открыть для российских предпринимателей неискушённые экспортные рынки, что особенно важно в условиях растущей конкуренции.
С учётом перечисленных факторов эксперты металлургической области ожидают, что закаливание металлических изделий в России будет развиваться дальше и находить всё новые применения в различных отраслях.
Технологии закалки
Закалка – это процесс термической обработки, который включает разогрев металла до критической температуры (от 815 до 870 °C), а затем его быстрое охлаждение. Основная цель закаливания – повышение углерода в железе. В процессе нагрева происходит аустенитизация – превращение структуры стали в аустенит, который обладает высокой пластичностью.
Быстрое охлаждение (обычно с использованием воды, масла или специальных солевых растворов) приводит к образованию мартенсита – микроструктуры высокой твёрдости. Весь процесс сопровождается изменением внутренних напряжений и конституции материала, что в конечном итоге влияет на его эксплуатационные характеристики.
Существуют различные технологии полной и частичной закалки, включая изотермическую, индукционную, лазерную, плазменную и криогенную. Все они могут придать металлу разные механические свойства.
1. Изотермическая закалка
Изотермическая термообработка представляет собой процесс, при котором металл нагревается до определённой температуры, а затем выдерживается в раскалённом состоянии в течение заданного времени. После этого заготовку быстро охлаждают. Этот метод позволяет достичь более равномерного распределения твёрдых фаз в структуре металла, что приводит к улучшению его механических свойств.
Преимущества технологии для заготовки:
- Повышение ударной вязкости и прочности.
- Возможность закалки сложных форм изделий.
- Уменьшение внутренних напряжений, что снижает риск деформации.
Области применения. Изотермическая закалка часто используется для обработки инструментальных сталей и сплавов, где требуется высокая прочность и износостойкость.
2. Индукционная закалка
Индукционная закалка основана на использовании электромагнитного поля для нагрева металлических изделий. В этом процессе ток проходит через катушку индукции, создавая магнитное поле, которое вызывает тепловые эффекты в металле. После достижения необходимой температуры изделие подвергается быстрому охлаждению.
Преимущества:
- Минимальные затраты энергии.
- Высокая скорость процесса закалки.
- Локальное нагревание, что позволяет обрабатывать лишь определённые участки заготовки.
Области применения. Индукционная закалка широко используется в автомобильной и машиностроительной отраслях для обработки деталей, таких как валы, шестерни и оси.
3. Плазменная закалка
Плазменная термообработка представляет собой метод, при котором металл нагревается с помощью плазменной дуги. Этот способ обеспечивает высокую скорость нагрева, что позволяет быстро раскалять заготовку до необходимой температуры.
Преимущества технологии:
- Высокая температура нагрева, что позволяет закаливать даже толстостенные изделия.
- Возможность термообработки сложных форм и конструкций.
- Устойчивость к термическим деформациям.
Области применения. Плазменная закалка применяется в высоконагруженных деталях, таких как компоненты турбин, насосов, коробок передач.
4. Лазерная закалка
Лазерная технология закаливания основана на использовании лазерного излучения для локального нагрева поверхности металла. Энергия луча подаётся непосредственно на обрабатываемый участок и нагревает его до температуры >1000 °C. Для точности фокусное пятно направляются роботом (в большинстве случаев). Это позволяет контролировать глубину и скорость нагрева, что приводит к высокой чёткости обработки.
Преимущества:
- Высокая скорость и точность процесса.
- Возможность обработки сложных геометрических форм.
- Минимальное термическое воздействие на окружающие участки изделия.
Области применения. Лазерная закалка используется в производстве высококачественных инструментов, а также в авиационной и космической промышленности для обработки деталей, требующих высокой прочности и износостойкости.
5. Криогенная закалка
Криогенная закалка включает в себя термическую обработку металлических изделий при t +150–650 °C после очень низких температур, обычно ниже -196 °C. В качестве охлаждающей среды используется жидкий азот. Сначала заготовка выдерживается в камере от 8 до 24 часов, а затем помещается в печь. Этот метод позволяет достигать значительных изменений в зернистой структуре металла, что приводит к улучшению его механических свойств.
Преимущества:
- Устранение внутренних напряжений и микротрещин.
- Повышение твёрдости и износостойкости.
- Увеличение срока службы изделий.
Области применения. Криогенная закалка находит применение в производстве инструментов, подшипников и других деталей, работающих в условиях высокой нагрузки и износа.
Разновидности оборудования
Многообразие оборудования для термической обработки металлических изделий определяется различными факторами, включая тип обрабатываемых заготовок, объёмы производства и требуемые характеристики термического воздействия. Назовём самые распространённые установки, используемые сегодня металлообработчиками для закаливания своих продуктов.
Изотермические печи
Используются для нагрева деталей до нужной температуры. Они могут быть электрическими и газовыми, в зависимости от технологии и конструкционных особенностей. Бывают горизонтальными и вертикальными.
Индукционные печи
Позволяют быстро нагревать металл за счёт электромагнитного поля. Это оборудование подходит для закалки мелких деталей и обеспечивает высокую точность обработки. Для эффективной работы индукционных тигельных печей приходится питать их токами повышенной, а в отдельных случаях и высокой частоты от соответствующих преобразователей тока.
Лазерные закалочные машины
Лазерная закалочная машина для поверхностной закалки стали литейных форм всё чаще используется в точечной термической обработке.
Плазменные закалочные печи
Камеры с технологией азотирования плазмой – это энергосберегающие и экологически безопасные установки. Они обеспечивают точный и эффективный процесс поверхностной термообработки, который необходим для поверхностного усиления отвественных деталей и инструментов.
Криогенные камеры
Представляют собой новую концепцию быстрого охлаждения, в которой в качестве хладагента используется азот. Машина может генерировать отрицательные температуры в диапазоне от -40 до -196 °C. После глубокой заморозки изделие нагревается до +149 C°. Камеры термического шока или термоциклирования позволяют быстро перемещать заготовки между экстремальными температурами, поочерёдно нагревать и охлаждать детали.
Оборудование для охлаждения
Ванны с охлаждающими жидкостями (вода, масло, полимерные растворы) являются неотъемлемой частью закалочного оборудования. Они представлены на рынке развёрнутым ассортиментом. Выбор охлаждающей среды зависит от требуемых свойств закалки и типа стали.
Особенности закалки различных видов стали и цветных металлов
Разные виды металлов требуют различных подходов к закалке, в зависимости от их химического состава, структуры и желаемых механических свойств. Некоторые стали могут содержать большое количество легирующих элементов, влияющих на их структурные свойства. Среди таких составляющих:
- хром,
- никель,
- углерод,
- молибден.
Поэтому углеродистые стали требуют одной температуры закалки и охлаждения, в то время как легированные стали могут требовать других условий из-за более сложного состава.
Ещё разные виды стали имеют различные микроструктуры (феррит, перлит, мартенсит). Закалка меняет конституцию материала для достижения желаемых свойств (например, твёрдости или пластичности) при контролируемом процессе нагрева и охлаждения. Также могут быть разные требования к прочности и вязкости:
- для инструментальных сталей важно достичь высокой твёрдости,
- для конструкционных может быть важнее сочетание прочности и пластичности.
В процессах учитываются требования к способам шокового охлаждения: в воде, масле или на воздухе. Они влияют на скорость остывания заготовки и, соответственно, на конечные свойства изделия. Форма и размеры деталей также имеют решающее значение для выбора метода термической обработки. Например, большие и толстые метизы требуют медленного охлаждения, чтобы исключить риски внутренних напряжений и трещин.
Таблица 1. Особенности закалки различных видов стали и цветных металлов
Металл | Особенности закалки |
Углеродистые стали | Требуют высокой температуры нагрева (обычно 800-900 °C) и быстрого охлаждения в воде или масле для достижения оптимальных свойств. Чувствительны к трещинообразованию при закалке, особенно при высоком содержании углерода. Но чем выше содержание углерода, тем выше потенциальная твёрдость |
Легированные стали | Закалка производится аналогично углеродистым сталям, но температура нагрева и охлаждение могут варьироваться в зависимости от легирующих элементов. Легирующие элементы помогают избежать трещинообразования и улучшают свойства при высоких температурах |
Нержавеющие стали | Часто требуют специальных режимов закалки, чтобы избежать образования хрупких структур. Не все нержавеющие стали могут закаливаться в традиционном понимании этого процесса (мартенситные – да, аустенитные и ферритные – нет) |
Титан | Этот металл не поддаётся традиционному закаливанию, как сталь. Вместо этого для улучшения механических свойств часто используется нагрев до высокой температуры с последующим медленным охлаждением. Закалка титана требует контролируемых условий, чтобы избежать образования хрупких фаз и сохранить пластичность |
Алюминий | Может быть закалён путём традиционной термической обработки, включая нагрев до 450-500 °C и быстрое охлаждение в воде или на воздухе. После термообработки часто проводится старение (естественное или искусственное) для улучшения механических свойств |
Медь | Не требует закалки в традиционном понимании, как сталь. Однако для улучшения механических свойств могут применяться процессы отжига при t 580-630°С, с выдержкой при данных температурах, и последующим остыванием на воздухе |
Латунь | Также не поддаётся закаливанию, но может быть обработана термически при t 450-650° С для улучшения прочности. Процесс включает нагрев и последующее медленное охлаждение. Закалённые метизы из латуни теряют пластичность |
Обработчики учитывают все перечисленные факторы и подбирают соответствующие режимы закалки для достижения оптимальных свойств готовых изделий. Иначе высока вероятность забраковать дорогостоящую заготовку или деталь, ухудшив её механические свойства выбором неправильной температуры нагрева и времени выдержки. Закалка - это не простое «нагрел-охладил», а тонкая технологическая операция.
Успешные кейсы
Изучение успешных практик может служить платформой для обмена опытом и лучшими компетенциями в области закалки метизов. Такая информация помогает выявить текущие тенденции и потребности рынка, позволяя нерешительным компаниям смелее адаптировать свои стратегии. А некоторых это может вдохновить на внедрение инновационных методов и технологий, что способствует развитию отрасли в целом.
Предлагаем обзор на 2 успешных кейса закалки метизов.
ММК-МЕТИЗ
Магнитогорский метизно-калибровочный завод ОАО «ММК-МЕТИЗ» заметил в отчётных показателях, что, помимо стабильного спроса на машиностроительный крепёж общего назначения в 140 тыс. т в год, существенно выросло количество заявок на высокопрочный крепёж. Даже образовалась тенденция замещения объёмов обычного крепежа на высокопрочный.
Учитывая заинтересованность клиентов, ММК-МЕТИЗ приобрёл в 2022 г. большую современную линию с конвейерными печами для закалки и отпуска крепёжных изделий. Это позволило заводу увеличить выпуск высокопрочного крепежа на 5,4 тыс. т в год и повысить общую доходность.
ОСПАЗ
Орловский сталепрокатный завод с 2018 года заметно увеличивает объёмы производства высокопрочного крепежа после запуска третьего термозакалочного агрегата San Yung (Тайвань). В рамках инвестиционной программы предприятие вложило около 140 млн рублей в приобретение нового оборудования, что в результате помогло нарастить объёмы производства метизов до 400 тонн в месяц.
Заключение
Закалка метизов – это важный технологический процесс, значительно повышающий эксплуатационные характеристики изделий. Несмотря на высокую стоимость закалочного оборудования, его использование оправдано в условиях, требующих высокой прочности и надёжности деталей. Выбор подходящей технологии и оборудования зависит от множества факторов, включая тип металла и требования к конечному продукту. Инвестирование в закалку – это инвестиция в надёжность и долговечность вашей продукции, что в конечном счёте расширит круг потребителей из разных отраслей промышленности.
Покупатели встанут в очередь за вашими метизами! Покупайте оборудование для закалки метизов в компании Eurasia Group. Узнать условия приобретения и доставки в регионы РФ можно по номеру бесплатного телефона 8-800-700-45-24 или через форму обратной связи.
Звоните! Пишите! Покупайте!