Оборудование для изготовления zip-lock пакетов с бегунками – технология и перспективы бизнеса
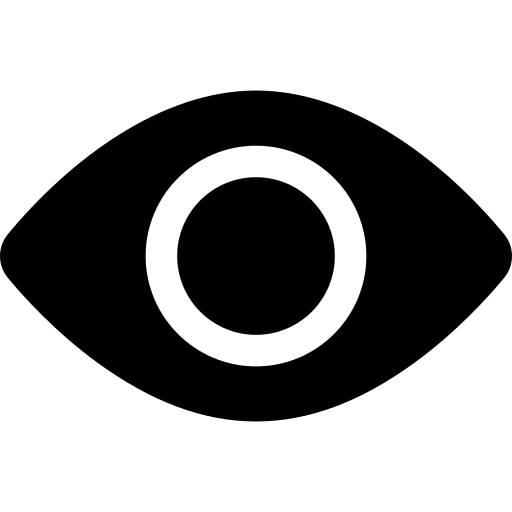
Zip-Lock пакеты существуют чуть более полувека, но сегодня вы найдёте их повсюду. И действительно, у них есть тысяча и одно практическое применение. Эти вездесущие многоразовые зип-пакеты повсеместно используются для упаковки, хранения и транспортировки продовольственных и непродовольственных товаров. Их практичность и особый тип замка позволили им решать самые востребованные и популярные упаковочные задачи, как для потребителя, так и для производителя. Поэтому предлагаем рассмотреть оборудование для изготовления ziplock-пакетов с бегунками, а также оценить актуальность бизнеса по их производству.
Zip-lock в переводе с английского означает «застёжка-молния». Сегодня это нарицательное название, особенно в РФ. Но существует бренд Ziploc®, принадлежащий американской компании S.C. Johnson & Son, Inc.
Кратко о назначении, преимуществах и видах zip-lock пакетов
Пакет зип-лок представляет собой категорию универсальной упаковки. Поэтому широко используется для расфасовки разнообразных товаров, от пищевых продуктов до промтоварных и медицинских изделий. По статистике 90% продавцов упаковывают те или иные виды продукции в пакеты с застёжкой-молнией. И это небезосновательно, ведь у них есть ряд неоспоримых преимуществ, таких как:
- Удобство.
- Практичность.
- Экономичность.
- Лёгкость и прочность.
- Герметичность и влагостойкость.
Пакеты zip-lock также называют грипперами, от слова grip – запирать.
По типу закрытия они делятся на 3 вида:
- Одинарные – с одной молнией.
- Двойные – с двойной молнией.
- Слайдерные – с бегунком.
Последний тип упаковки закрывается при помощи слайдера. Данное приспособление облегчает прижим частей замка-молнии. По сути это бегунок, который обеспечивает равномерное прилегание шипа и паза по всей длине пакета.
Оценка актуальности производства zip-lock пакетов
Востребованность. Большинство производителей продуктовых, промышленных и медицинских товаров, а также кормов для животных, – серьёзно интересуются упаковкой типа zip-lock. Поэтому ассортиментная линейка пакетов с застёжкой-молнией сегодня очень развёрнутая. Она выросла стремительно, под давлением высокого спроса. Но даже такой широкий выбор не может удовлетворить всех потребителей.
В результате одни покупают стандартные зипперы, другие заказывают индивидуальные. В последнем случае новая разработка становится толчком к развитию стандартной упаковки, которую можно улучшать до бесконечности, руководствуясь требованиями клиентов. При этом оставляя главный элемент конструкции – застёжку zip-lock.
Экологичность. Сегодня очень силён тренд на экологичное потребление и вторичную переработку. Это обстоятельство оказывает непосредственное влияние на актуальность бизнеса по изготовлению zip-lock пакетов. Ведь в производстве можно использовать первичные и вторичные гранулы полимеров:
- Первичные – для продуктов питания и медицинских препаратов.
- Вторичные – для промышленных товаров.
Предприятие с приставкой «эко» пользуется привилегиями государства и выполняет важную природозащитную функцию – использует вторсырьё. Его можно производить самостоятельно из пластиковых отходов или бракованных зипперов, или закупать на перерабатывающих предприятиях.
Импортозамещение. Россия ввозит значительную часть зиплоков из-за границы. Основными экспортёрами полиэтиленовых пакетов и мешков выступают азиатские, восточные и европейские страны, такие как:
- Китай (43,36%).
- Азербайджан (12,40%).
- Вьетнам (11,51%).
- Корея (5,94%).
- Беларусь (4,65).
Много закупали в Германии, Италии и Финляндии. Поскольку отечественные производители не могут полностью удовлетворить спрос, так как не обладают для этого достаточными производственными мощностями. Поэтому рынок нуждается в российских грипперах.
Перспективы организации производства zip-lock пакетов в регионе
В каждом городе страны сегодня можно встретить развитую торговлю. Это продуктовые сети, строительные магазины, аптеки, точки общепита и многое другое. Чуть менее развито производство штучных товаров (говорим о повсеместности). Тем не менее, все производители и продавцы пользуются пакетами zip-lock для расфасовки продукции.
Особенную популярность зипперы получили с 2020, в пик развития e-com (электронной торговли) из-за пандемии. Продавцы с Wildberries, Ozon, Яндекс Маркет и других маркетплейсов высоко оценили практичность многоразовых грипперов, и вот почему: покупатели возвращали товар в неповреждённой упаковке, потому что у неё есть замок-молния.
Поэтому перспективы организации производства зиплоков многообещающие в любом мало-мальски развитом крае. Объёмы выпуска пакетов обуславливает плотность населения города или региона. Например, компания ООО «ПакПром» из г. Бердск Новосибирской области выпускает 0,5–1 млн пакетов zip-lock ежедневно. Количество зависит от толщины плёнки (20–100 мкм). Почти все они предназначены для закупщиков, профилирующих на медицине и фармакологических товарах.
Полный цикл производства zip-lock пакетов
Пакеты zip-lock с бегунком состоят из трёх элементов: пакета, молнии и слайдера. Каждый из них изготавливается отдельно, после чего конструкция зиппера собирается на пакетосварочной машине. В целом получается 4 этапа.
Производство плёнки для пакетов
Изготовление плёнки для пакетов осуществляется на выдувном экструдере. Это аппарат щелевой экструзии с вертикальной воздушной камерой, в которой материал приобретает форму рукава. Поэтапно это выглядит так:
- Пластиковые гранулы засыпают в приёмный бункер экструдера.
- Из бункера гранулы поступают в нижнюю камеру, где нагреваются до вязкого состояния и перемещаются шнеком к формовочной головке.
- Горячий расплав выталкивается шнеком через кольцевую головку в воздушную камеру, образовывая при этом материал рукавной формы.
- Далее рукав подхватывается воздухом и раздувается изнутри до нужных размеров, после чего охлаждается и соединяется в двойную плёнку.
- Охлаждённый полиэтиленовая плёнка наматывается на бобину, образовывая рулон.
Рулон с рукавным полиэтиленом готов к изготовлению пакетов. Но его могут дополнительно украсить рисунком, логотипом компании или рекламной информации. Для этого рулон прогоняют через флексографическую высокоскоростную машину.
Производство зип-ленты
Этот элемент грипперов тоже изготавливается на экструдере. Но здесь расплав проталкивается через плоскощелевую формовочную головку с формами шип/паз в центре. Далее детали охлаждаются и соединяются. После этого готовую зип-ленту сматывают в катушку.
Производство бегунка (собачки)
Бегунок также изготавливается методом экструзии. Расплав полимеров выталкивается шнеком через головку с формой слайдера. Далее полоску охлаждают и нарезают на бегунки. Затем «собачки» упаковывают в коробки и отправляют на склад.
Сборка пакетов на пакетосварочной машине
Сборка зипперов проходит на пакетосварочной машине с относительно высокой скоростью. На станок устанавливаются: 1) рулон с рукавной плёнкой; 2) рулон с молнией; 3) контейнер с бегунками. Размотчик разматывает рукав и подаёт его в операционную зону. Сюда же подаётся молния. Здесь материалы свариваются, образуя длинное полотно с зип-молнией. Далее специальный автомат вставляет в молнию собачку, через определённое расстояние. Затем полотно нарезается по размеру на пакеты. Их края спаиваются, а получившееся готовое изделие откидывается на сборочный стол.
Из какого сырья делается плёнка, зип-лента, собачки для zip-lock
Зипперы изготавливаются из полиэтилена. Но для каждого элемента используется определённая марка пластика:
- Плёнка – ПВД (полиэтилен высокого давления) и ПП (полипропилен).
- Молния – ПВД (полиэтилен высокого давления) и ПП (полипропилен).
- Собачка – ПВХ (поливинилхлорид) и ПП (полипропилен).
Закупать полиэтиленовые гранулы можно у поставщиков на оптовых базах или прямо на комбинатах по переработке пластика. Или брать у производителей готовые элементы: рукавную плёнку, молнию и бегунки (если ваша компания занимается только сборкой пакетов).
Оборудование для производства пакетов zip-lock
Предлагаем краткий обзор пяти машин для изготовления грипперов с бегунками, из которых можно собрать парк техники предприятия полного цикла: от изготовления плёнки и молний с бегунками, до флексографической печати и сварки пакетов.
Экструдер для производства полиэтиленовой плёнки CH-E800
Машина изготавливает полиэтиленовую рукавную плёнку из гранулированного сырья методом экструзии – выдавливания расплава через кольцевую головку, и раздува материала через спиральную фильеру. Максимальная ширина выпускаемой плёнки 800 мм, а толщина от 0,008 до 0,12 мм. Готовый рукав сматывается в рулон и представляет собой исходный материал для производства пакетов.
Модель | CH-E800 |
Максимальная ширина плёнки (мм) | 800 |
Производительность (кг/ч) | 45-50 |
Материал плёнки | HDPE, LDPE, LLDPE |
Толщина плёнки | 0.008-0.1 |
Диаметр комплектных голов (мм) | 60,120 (150-опционально) |
Диаметр выдувного кольца | 780 |
Отношение длины шнека к диаметру | 28:1 |
Диаметр шнека (мм) | 55 |
Материал шнека | 38CrMoAlA |
Скорость вращения шнека (об/мин) | 10-80 |
Мощность основного двигателя (кВт) | 15 |
Мощность нагрева (кВт) | 18 |
Валы намотки | Пневматический |
Количество постов намотки | 1 (2-опционально) |
Система смены рулонов | Механическая (автоматическая-опционально) |
Напряжение (В)/ Частота (Гц) | 380/50 |
Габаритные размеры (мм) | 4500 x 2200 x4500 |
Вес (кг) | 2500 |
Активатор плёнки CV-8/20 (Коронатор)
Машина для обработки плёнки коронным зарядом. Ещё этот этап обработки называют активацией плёнок. Благодаря ему, поверхностное натяжение полиэтилена увеличивается, тем самым обеспечивая лучшее сцепление с поверхностью краски, типографического покрытия или клея. Ещё обработка коронным разрядом увеличивает проницаемость полиэтиленовых и полипропиленовых плёнок, чтобы способствовать лучшей адгезии печатных красок, чернил, лаков или других покрытий. Данное устройство не является самостоятельным станком, а устанавливается на экструдер или печатную машину.
Модель | CV-8 |
Максимальная ширина плёнки | 800 мм |
Мощность | 2 кВт |
Вес | 30 кг |
Габаритные размеры | 1000 х 200 х 150 мм |
Двухцветная машина для флексопечати XQI-2-600
Модель представляет собой промышленный высокоскоростной печатный станок. Обеспечивает идеальное качество нанесение красок на упаковочные материалы, такие как полиэтилен, полипропилен, целлофан, различная рулонная бумага и т.д. Скорость печати от 5 до 50 метров в минуту.
Модель | XQI-2-600 |
Максимальная ширина материала (мм) | 600 |
Максимальная ширина печати (мм) | 560 |
Диапазон печати по длине (мм) | 191 ~ 914 |
Максимальный диаметр рулона материала (мм) | Φ 450 |
Скорость печати (м/мин) | 5 ~ 50 |
Толщина пластины (мм) | 2,38 |
Общая мощность (кВт) | 8 |
Габаритные размеры (мм) | 2300 х 1860 х 2145 |
Вес (кг) | 1800 |
Экструдер для производства ZIP-LOCK застёжки ZL-45
Мини-линия непрерывного действия для малых и средних промышленных предприятий. Непосредственная задача – изготовить элемент в виде скрепляемой вручную дорожки, которая в процессе изготовления пакетов присоединяется к полиэтиленовому полотну. Комплекс оборудования разделён на 5 нагревательных зон и оснащается шнеком из высокопрочной стали, стойкой к длительным нагрузкам и повышенной температуре. Станция наматывания с одной катушкой имеет подвижную подачу с направляющим бегунком, которая равномерно распределяет полученную ZIP дорожку на катушке.
Модель | ZL-45 |
Материал | ПВД, ПП |
Производительность (м/мин) | 10-50 |
Ширина молнии (мм) | 3-50 |
Толщина молнии (мм) | 0.3-2.2 |
Диаметр шнека (мм) | 45 |
Отношение длины шнека к диаметру (мм) | 25:1 |
Мощность главного двигателя (кВт) | 5.5 |
Мощность вспомогательного двигателя (кВт) | 1.1 |
Мощность сушки (кВт) | 2 |
Мощность намоточного устройства (кВт) | 1.1 |
Мощность нагревателей (кВт) | 6.8 |
Общая мощность (кВт) | 22 |
Габаритные размеры (мм) | 9350 x 1300 x 2200 |
Станок для изготовления пакетов c застёжками молниями (ZIP-LOCK) ZL-Q-800
Машина для производства пакетов c застёжками молниями ZIP-LOCK представляет собой многофункциональную линию оборудования с цифровой системой программирования. Предназначена для массового выпуска грипперов в условиях средних и крупных промышленных предприятий. Прочная и надёжная конструкция, сформированная по модульному принципу, рассчитана на длительную безостановочную работу.
Процесс спаивания происходит с помощью ультразвуковой линейной сварки. На ровном участке протягивания пакет подвергается перфорированию вертикальным электропневматическим дыроколом. Далее на молнию-застёжку вставляется бегунок. Эту операцию выполняет вибрационный питатель типа «улитки» и инструмент фиксации. Затем каждый пакет отрезается от полотна термоножом, его швы свариваются, после чего готовое изделие покидает операционную зону. За автоматизацию процесса отвечает ПЛК, а диалог машины с оператором осуществляется через цветной сенсорный экран DELTA.
Модель | ZL-Q-800 |
Материал плёнки | PE / PP |
Производительность (шт. /мин) | 40 ~ 80 |
Ширина пакета (мм) | 100 - 550 |
Длина пакета (мм) | 100 - 650 |
Толщина пакета (мм) | 0,04 – 0,15 |
Мощность сервопривода (кВт) | 2 |
Мощность основного двигателя (кВт) | 1,5 |
Мощность ультразвуковой пайки (кВт) | 2 |
Мощность устройства подачи (кВт) | 0,75 |
Мощность охладителя (кВт) | 0,8 |
Общая мощность (кВт) | 15 |
Питание (В / Гц) | 380 / 50 |
Габаритные размеры (мм) | 8500 х 1650 х 1800 |
Вес (кг) | 3500 |
Представленное в обзоре оборудование изготавливается в Китае. Это сертифицированные машины, не уступающие по качеству аналогам из США, ЕС, Южной Кореи и Японии. Зато цена китайских станков заметно ниже, чем у конкурентов из развитых стран.
Заключение
Zip-Lock пакеты – это невероятно удобная многоразовая мягкая тара, способная решать различные упаковочные задачи. Последнее время она пользуется повышенным спросом со стороны продавцов e-com. Одинаково хорошо подходит для пищевых, промышленных, медицинских и других товаров. Ежегодное потребление зиплоков только в России исчисляется миллиардами штук.
P.S.
История ZIPLOCK
В 1951 году изобретатель Борге Мэдсен получил патент на пластиковый пакет с застёжкой-молнией. Она стала предшественницей известной сегодня концепции ziplock. Дизайн прототипа был немного сложнее, чем текущая версия замка-молнии с бегунком – у него было две «зоны взаимодействия» вместо одной, используемой сегодня, и он больше походил на традиционную молнию с язычком, за исключением того, что у неё не было зубцов и она была сделана из пластика.
В том же 1951-м появилась компания Flexigrip с целью массовой разработки и продажи продукта Мэдсена, чьи патенты она приобрела. Сначала ziplock применяли в скоросшивателях с вкладными листами, в портфелях и папках. Но высокие затраты на производство пластиковых застёжек-молний с язычком не позволяли продукции выйти на рынке пакетов и конкурировать по стоимости. Поэтому они не завоевали потребителя в широком охвате.
Затем Стивену Осниту, одному из основателей семейной компании Flexigrip, пришла в голову идея застегнуть молнию простым нажатием. Так появилась концепция «вжимай и застёгивай». Именно этот тип замка получил широкое распространение во всём мире и дошёл до нас в исходном формате.
В те времена промышленности приходилось отдельно закупать замки и присоединять их к пакетам. Готовую продукцию называли «пакеты с молниями» или «пакеты с застёжкой». 18 мая 1954 года Flexigrip лицензировала зипперы с бегунком, как пакеты для карандашей.
Самая революционная функция гриппера была реализована в 1957 году. Тогда пятиклассник по имени Роберт Лежен продемонстрировал, что в пакете из-под карандашей с бегунком можно удобно и безопасно носить в школу сэндвичи для лёгкого перекуса. Его примеру последовали одноклассники, затем вся школа, а далее идея получила промышленное развитие.
Ещё один большой скачок в развитии ziplock произошёл в 1959 году. Тогда Оснит узнал о японской компании Seisan Nihon Sha, которая разработала новый производственный процесс, позволяющий экструдировать профили с застёжкой-молнией в полиэтиленовую плёнку. Это была инновация, которая вдвое сокращала производственные затраты. В отрасли они назывались «пакеты со встроенной застёжкой» или «пакеты со встроенной молнией».
В 1961 году Flexigrip получила лицензионные права на «интегральные молнии» и основала другую компанию под названием Minigrip для продажи недорогих пакетов с застёжкой. Minigrip в первую очередь ориентировалась на промышленные пакеты с фирменным знаком RED LINE™ — тонкой «красной линией» над молнией.
Примерно в 1964 году Minigrip заключила эксклюзивное лицензионное соглашение с Dow Chemical Company на продажу пакетов с застёжкой-молнией через продуктовые магазины и супермаркеты. Уже знакомый потребительский бренд Ziploc был запущен и широко продавался в 1968 году. Ему потребовалось пару лет, чтобы завоевать популярность. К началу 1970-х фирменные пакеты Ziploc стали чрезвычайно востребованными потребителями буквально для всего: от хранения бутербродов для школьных обедов до перевозки золотых рыбок домой из зоомагазина.
В 1978 году Minigrip перешла под управление компании Signode, Inc. А через 10 лет Signode была приобретена ITW, и Minigrip стала её дочерней компанией. В 1997 году Dow Chemical продала права на бренды Dow, включая Ziploc, компании SC Johnson за $1,7 млрд.
В «нулевых» на рынок начали выходить другие потребительские бренды. Среди них Hefty, Glad-Lock и прочие частные супермаркеты. Они стали продавать свои пакеты с молниями, отказавшись от концепции RED LINE™, поскольку ещё в середине 1980-х истёк срок действия оригинальных патентов Minigrip на «встроенную молнию». Тем не менее бренд Ziploc остался самым крупным и известным из всех потребительских пакетов с застёжкой-молнией.
До 2006 года холдинг ITW Minigrip производил всю линейку промышленных изделий RED LINE™ на заводе в Сегине, штат Техас. Но компания стремительно теряла рынок, потому что многие промышленники начали импортировать пакеты аналогичного типа из Китая и других частей Азии из-за более дешёвого производства и стоимости.
Чтобы конкурировать с потоком импортных пакетов, ITW Minigrip купила завод в Таиланде и в 2006 году перенесла туда производство всех своих промышленных пакетов с замком на молнии. В период с 2008 по 2011 год ITW Minigrip начала приобретать некоторых крупных импортёров, стремясь консолидировать рынок. В 2012-м Минигрип была приобретена Группой «Интепласт», крупным производителем США и импортёром всех видов промышленных, розничных и медицинских полиэтиленовых пакетов.
В настоящее время Minigrip остаётся дочерней компанией североамериканского производителя – Inteplast Group. А брендом Ziploc по-прежнему владеет SC Johnson.