Как проверить качество обжима РВД и каким испытаниям подвергаются шланги?
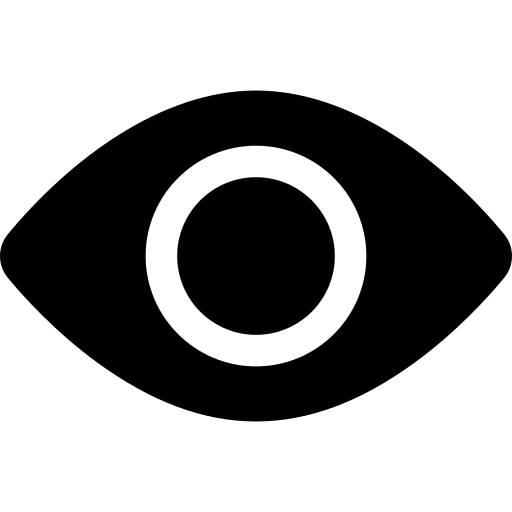
Рукава высокого давления (РВД) широко используются в технике с гидравлическими, пневматическими и паровыми механизмами. Надёжная работа этих узлов и безопасность персонала во-многом зависят от качества шлангов. Поэтому в продажу они поступают только после ряда испытаний на герметичность и прочность, под разными нагрузками и в различных температурных режимах. Порядок проверок регламентирован ГОСТ 6286-2017. Забегая вперёд скажем, что из каждой партии РВД должно тестироваться не менее 5% выпущенной продукции, а эксплуатируемые шланги надлежит проверять время от времени в процессе технического обслуживания. Ниже вы ознакомитесь с методами испытаний РВД. Данная информация окажется полезной, если вы планируете заняться производством рукавов высокого давления, или эксплуатируете технику с гидравлическими, пневматическими или паровыми узлами.
Испытания делятся на 2 категории: приёмо-сдаточные и периодические. Первые проводит изготовитель, а вторые – эксплуатирующая организация.
Зачем проверять шланги РВД
Рукава высокого давления работают под нагрузкой. Напор масла или воздуха способны разорвать резиновый шланг, даже армированный, особенно в условиях внезапной перегрузки. В момент разрыва могут пострадать люди (в истории много случаев, когда сотрудники получали травмы). Аварийная ситуация не позволит продолжать работу. Предстоит останавливать машину и менять рукав. А простой техники влечёт убытки.
Чтобы снизить риски имущественного и физиологического вреда необходимо ставить надёжные шланги, прошедшие все степени проверки. К тому же время от времени персонал должен проводить техническое обслуживание гидравлических или пневматических узлов, в рамках которого также требуется тестировать РВД. Периодичность проверки шлангов зависит от их видов.
Виды шлангов РВД
В настоящее время на рынке многообразие рукавов высокого давления. Каждый из них отвечает стандартам качества и утверждён ГОСТ. В основном РВД делятся по типу конструкции на 2 вида:
- Оплёточные.
- Навивочные.
Оплёточный тип самый распространённый. Выпускается по стандартам EN 853 и EN 857 (аналоги ГОСТ 6286-73). Предназначен для работы с гидрожидкостями, утверждёнными в международном ГОСТ ISO 6743-4. Классифицируется на следующие подвиды:
- 1ST – с одной оплёткой из латунированной проволоки.
- 2ST – с двумя оплётками из латунированной проволоки.
- 1SC и 2SC – для кранов, с меньшим радиусом изгиба, чем 1ST и 2ST.
- 3SK – для высоких импульсных нагрузок, чем могут выдержать 1SC и 2SC.
- 1SN – с одной оплёткой и более тонким слоем резины.
- 2SN – с двумя оплётками и более тонким слоем резины.
Температурные режимы работы от -70°C до +70°C. Периодичность проверки 1–5 лет, в зависимости от условий эксплуатации.
Навивочный тип рукава высокого давления выпускается для эксплуатации в условии средних и тяжёлых давлений. Он обладает повышенным сроком службы. В конструкции этих шлангов есть спиральные навивки стальной проволоки. Качество продукции регламентируется стандартом EN 856. Навивочные шланги классифицируются на 4 подвида:
- 4SP – с четырьмя спиральными навивками для средних давлений.
- 4SH – с четырьмя спиральными навивками для высоких давлений.
- R12 – с четырьмя спиральными навивками для высоких температур и средних давлений.
- R13, R15 – с многоспиральными навивками для тяжёлых условий эксплуатации (высокое давление, импульсные нагрузки).
Навивочные РВД характеризуются хорошей устойчивостью к максимальному рабочему давлению, повышенным уровнем минимального разрывного давления и надёжной герметичностью. Легко выдерживают 400–500 тыс. циклов при температуре 100°С. Часто встречаются на иностранной спецтехнике: Caterpillar, Case, Claas, John Deere, JCB, Komatsu, New Holland, Volvo, Manitou, Hitachi и Hyundai. Периодичность проверки навивочных РВД 5 лет (ГОСТ 25452-90).
Значение разрывного давления – это контрольные точки результата испытаний, благодаря которым определяется сопротивление РВД. Ведь в процессе работы система может подвергаться импульсным напорам. При таких условиях шланг переносит усиленный натиск гидравлического масла или воздуха, намного выше номинального, что сокращает срок его службы.
Изготовители оборудования с гидравликой или пневматикой утверждают, что выбранные ими шланги для сборки техники соответствуют заявленным параметрам производительности и срокам службы, и даже могут превосходить их. Поэтому предлагают с технической документацией регламент обслуживания, где шлангам отведена отдельная глава с рекомендациями проверки и замены. Дело в том, что технологии не стоят на месте и в разработке новых машин инженеры стараются применять РВД с более высокими уровнями производительности и надёжности.
Проще говоря они продвигают устойчивость шлангов высокого давления к запредельным стандартам производительности, что повышает срок службы техники. Это позволяет опережать конкурентов по некоторым эксплуатационным показателям. Так вот, чтобы рукава надёжно служили в неблагоприятных условиях, особенно при высоких температурах, технологи разрабатывают высококачественные каучуковые смеси и новые армирующие материалы, после чего вносят некоторые изменения в конструкции шлангов. Поэтому надо внимательно читать инструкцию производителя к проверке и тестированию РВД. Возможно она отличается от общепринятых регламентов, и в ней указаны надлежащие параметры тестирования.
Каждая партия РВД сопровождается документом о качестве – паспортом по форме, установленным изготовителем (п.4.4.5 ГОСТ 6286-2017).
Периодичность проверки РВД
Рукава высокого давления нельзя эксплуатировать за пределами утверждённых производителем температурных диапазонов. Это снижает герметичность заделки (соединения шланга с фитингом). Также не рекомендуется использовать в узлах РВД с характеристиками, близкими к максимальным температурным ограничениям. Это в свою очередь сократит срок службы резины и может повлечь аварийную ситуацию. Поэтому за шлангами необходимо следить и проверять их время от времени. Для надлежащей эксплуатации РВД утверждены свои сроки и регламенты проверки.
Испытания проходят под давлением, утверждённым в стандарте. Например, в ГОСТ 9356-75 для оплёточных рукавов есть таблицы, в которых перечислены:
- группы рукавов в зависимости от разрывного усилия (А, Б, В и Z);
- технические требования к изготовлению и правила приёмки РВД;
- процент выборки для проверки соответствия качества;
- методы испытаний на прочность, герметичность и др.
- периодичность проверки.
Таблица 1. Периодичность проверки оплёточных РВД по ГОСТ 9356-75.
Контролируемый показатель | Объём выборки РВД | Периодичность |
Стойкость к воздействию агрессивных сред | по 2 шланга из 2-х партий | 1 раз в 6 месяцев |
Морозостойкость | по 4 шланга от каждой группы и типа | 1 раз в 6 месяцев |
Динамические испытания | 2 шланга с фитингами разного размера | 1 раз в 12 месяцев |
Отклонение от перпендикулярности торца оси рукава | 2 шланга из партии | 1 раз в 6 месяцев |
Изменение длины рукава при рабочем давлении | по 2 шланга от каждой группы и типа | 1 раз в 3 месяца (в квартал) |
Новые РВД, не прошедшие испытаний, подвергаются повторным проверкам. При этом количество тестируемых шлангов может быть увеличено, или испытаниям подвергается вся партия (зависит от характера проводимой проверки: герметичность, прочность, увеличение длины и прочее).
Для справки. Герметичность заделки имеет двойной запас прочности. То есть, если рабочее давление 20 МПа (200 кг/см²), то соединение шланга с фитингом должно выдерживать 40 МПа (400 кг/см²).
Виды тестов
В тестах РВД крайне важно проверять не только шланги, но и фитинги. Обычно они испытываются в составе единой конструкции (заделки), на совместимость и долговечность. Полный цикл проверки сводит к минимуму потенциальные сбои. Это в свою очередь сокращает время простоя техники в случае аварии, повышает безопасность и снижает ущерб, вызываемый остановкой производственных циклов.
Какие испытания проходят РВД
Последовательное тестирование необходимо, чтобы не отставать от отрасли, находящейся в постоянном движении. Выборочные проверки позволяют сравнить шланги с разными отраслевыми стандартами и эталонами. Вот некоторые из движущих сил первичной экспертизы или повторного теста для эксплуатируемого РВД:
- Изменения материалов. Производители часто вносят изменения в свои материалы (резиновые и стальные), поскольку этого требуют современные эксплуатационные условия, а также внедрение новых компонентов в гидравлические жидкости и газы, протекающие через РВД.
- Изменения в производственном процессе. Из-за новых процессов опрессовки, качество и технологии которой могут отличаться в зависимости от типа оборудования, у шланга могут поменяться характеристики.
- Изменения условий эксплуатации. Любые перемены окружающей среды, переход на другой сорт гидравлики, смена температурного режима и метаморфозы с давлением, – могут повлиять на структуру РВД. Например, при условиях пониженной влажности резина имеет свойство рассыхаться.
- Недостатки в конструкции и заделке. Примерами таких дефектов являются ошибки в методике обжима и нарушение изгиба шланга или недостаточный радиус.
- Неправильная сборка. Бывают случаи, когда шланги и фитинги не предназначены для совместного использования. Например, для навивочных рукавов нельзя использовать фитинг с хвостовиком Multifit. Можно Interlock или CS.
- Ограниченное пространство. Защемление или трение во время работы может привести к выходу шланга из строя из-за эрозионного износа.
- Испытание на вибрацию. Механическая вибрация используется для имитации воздействия на РВД постоянного встряхивания.
Перечень тестов можно сократить, или наоборот – расширить. Это зависит от целевого назначения РВД. Согласитесь, нет смысла проверять шланг на правильность сборки, если заделку производили на вашем предприятии с соблюдением всех технологий.
Методика основных испытаний шлангов
Несколько ключевых процедур испытаний гидравлических и промышленных шлангов подпадают под действие стандартов EN 853, EN 856, EN 857, ГОСТ 9356-75, ГОСТ 25452-90 и других. Эти нормы сосредоточены на безопасности, экологических проблемах и на том, как шланги в сборе будут работать при различных нагрузках. Приёмо-сдаточные тесты могут исходить от производителей, которые поддерживают внутренний контроль, а также от дистрибьюторов, если у них есть свои стандарты для продаваемых шлангов. Важнейшие испытания включают в себя:
Проверку размеров — каждый шланг должен соответствовать размерам, указанным для своего типа или серии в паспорте. Такой тест считается первичным аудитом качества после производства.
Контрольные испытания/испытания на утечку — в этих тестах применяется давление в два раза превышающее максимально допустимое рабочее давление (МДРД). Это позволяет убедиться, что шланг не разорвётся, а заделки не будут протекать.
Изменение длины — когда шланг находится в пределах максимально допустимого рабочего давления, его величина не может превышать определённое процентное изменение, указанное в ГОСТе для этого типа РВД.
Испытание на разрыв — этот тест характеризуется постоянным повышением давления внутри шланга с фитингами до тех пор, пока не произойдёт его разрушение. Данная проверка определяет коэффициент запаса прочности рукава.
Холодный изгиб — при испытании на холодный изгиб шланг в сборе погружается в низкотемпературную жидкость, после чего скручивается в кольцо до минимального радиуса. Охлаждённый рукав не может протечь или разрушиться при давлении, указанном в стандартах для этого типа и размера РВД.
Импульсное испытание — Импульсное испытание производит толчки высокого и низкого давления на стенде, чтобы имитировать эксплуатацию машины с циклами включения/выключения.
Маслостойкость — исследования проводятся для подтверждения того, что шланг и материалы, из которых он изготовлен, могут выдерживать длительное воздействие используемой гидравлической жидкости.
Электрическая проводимость — шланги и фитинги проверяются на удельное электрическое сопротивление и проводимость, что во многих случаях продиктовано нормой безопасности.
Вакуум — не должно быть признаков вздутия или разрушения шланга через пять минут при абсолютном давлении, как указано стандартах качества.
Дополнительные тесты
В дополнение к основным испытаниям шлангов могут быть проведены добавочные тесты, если установка РВД планируется в машины для эксплуатации в особых условиях. Среди этих оценок:
Истирание изнутри — этот тест измеряет долговечность и срок службы шланга внутри, когда во время эксплуатации происходит трение транспортировочных материалов о резиновые стенки (например, цемент; химические продукты, абразивы и прочее).
Скорость старения — резина подвержена рассыханию (старению) при повышенных температурах или влиянию агрессивных сред (ультрафиолетовое излучение, химические испарения, воздействие озона в превышенных концентрациях от электрических установок). На специальных стендах ускоряют процесс старения резины, что может приблизительно определить время, которое потребуется для выхода РВД из строя.
Термоциклирование — оценивает поведение резины и фитингов при резком перепаде экстремальных температур. Пределы циклов и частота могут быть разработаны для точного воспроизведения условий эксплуатации.
В чём ценность испытаний РВД
Для потребителя проверки снижают риски покупки некачественных запчастей. Испытания качества позволяют компаниям принимать обоснованные решения о выборе поставщиков. В свою очередь изготовители сосредоточиваются на списке важных характеристик, влияющих на производительность шланговых систем, и стараются приблизить параметры к эталонным данным. В целом испытания помогают проверить согласованность конструкции РВД, убедиться в размерах, узнать свойства материалов и оценить общую производительность резины и фитингов. Это позволяет своевременно исключить производственные несоответствия и снизить риск аварийных ситуаций.
Заключение
Проверка шлангов имеет решающее значение для изготовителей, поставщиков и эксплуатантов РВД. Конечно, в обустройство испытательного цеха и покупку стендов потребуются вложения. Но вместе с этим собственная лаборатория гарантирует высокое качество выпускаемой продукции и снижает риски аварий на производстве.